CM445 CONTINUOUS MINER
The Cat® CM445 Continuous Miner is designed for mining applications ranging from 1626 mm (64 in) up to 3810 mm (150 in) where increased weight to horsepower ratios are required for performance in hard cutting type mining conditions. The hard head-style cutter head makes the CM445 the preferred miner for hard-cutting coal, trona, and potash.
SPECIFICATIONS
Mining Range1651-3480 mm (65-137 in)
Weight85.7 tonnes (189,000 lb)
Total Power884.0 kW
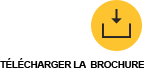
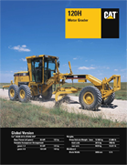
BENEFITS AND FEATURES
mainframe
LEARN MOREtraction
LEARN MOREcutter head
LEARN MOREspecifications
Mining Range1651-3480 mm (65-137 in)
Weight85.7 tonnes (189,000 lb)
Total Power884.0 kW
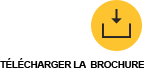
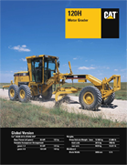
power
Cutter Head Power500.0 kW
Total Power884.0 kW
operating dimensions
Maximum Reach3785.0 mm
Ground Clearance229.0 mm
Length Rear Bumper to Face8631.0 mm
Minimum Height1499.0 mm
Mining Range (recommended)1651-3480 mm (65-137 in)
machine weight
Weight (total)85.7 tonnes (189,000 lb)
loading unit
Conveyor Depth305.0 mm
Conveyor Power - Motors (one-hour rating)2 × 48 kW (2 × 65 hp)
Conveyor Width965.0 mm
Loading Capacity14-35 tonnes/min (15-39 tons/min)
Loading Method3 finger CLA
optional dust suppression
Fan Power - Motor1 × 30 kW (1 × 40 hp)
Scrubber AssemblyTop mounted
Scrubber Capacity4.7 m3/sec (10,000 ft3/min)
Scrubber TypeWet bed
cutting unit
Cutting Drum Diameter1118.0 mm
Cutting Drum Width3581.0 mm
Cutting Power - Motors (one-hour rating)2 × 209 kW (2 × 280 hp)
total installed power
One-hour Rating without Scrubber727.0 kW
transport dimensions
Frame Width (over rub rails)3424.0 mm
Height (over cover line)1394.0 mm
Overall Length11530.0 mm
traction unit
Crawler Assembly Length3551.0 mm
Crawler Chain Width559.0 mm
Crawler Speed0-23 m/min (0-75 ft/min)
Ground Pressure212.0 kPa
Traction Power - AC/VFD (one-hour rating)2 × 82 kW (2 × 110 hp)
pump unit
Pump Power - Motor (one-hour rating)1 × 48 kW (1 × 65 hp)
electrical system
Control SystemProcessor based/radio remote control
Machine Voltage (International voltages available)995V AC 60 Hz
cutting
0 to Maximum Cut1492-3989 mm (58.75-157 in)
BENEFITS AND FEATURES
MAINFRAME
LEARN MORETRACTION
LEARN MORECUTTER HEAD
LEARN MOREGATHERING HEAD AND CONVEYOR
LEARN MORECONTROL SYSTEMS
LEARN MOREVFD TECHNOLOGY
LEARN MOREHEALTH AND SAFETY
LEARN MORESERVICEABILITY
LEARN MOREMOTEUR
BENEFITS AND FEATURES
Heavy Duty Mainframe To ensure maximum rigidity and stability, the high-strength one-piece mainframe is constructed from steel plate ranging in thickness from 1.9 to 7.6 mm (0.75 to 3 in). Large diameter, robust hinge points with replaceable hardened steel pins and bushings for the cutting head, gathering head and conveyor. The main support rails are 50.8 mm (2 in) thick, and the large 114.3 mm (4.5 in) diameter pivots have replaceable 12.7 mm (0.5 in) wall bushings. The mainframe has been shortened by 762 mm (2 ft 6 in) to improve maneuverability.
BENEFITS AND FEATURES
Traction Like all Cat continuous miners, the CM445 features independent tramming for greater maneuverability and wide crawlers for maximum penetration and low ground pressure.
Maximum Torque The traction system is controlled by Variable Frequency Drives (VFDs), which give smooth zero-to-full speed transition. The drives can develop 100% torque at zero RPM.
Crawlers Forged, heat-treated alloy steel pads with a minimum hardness of 340 BHN with a width of 558.8 mm (22 in) ensure high strength and wear resistance, and low ground pressure.
Enhanced Productivity Variable Frequency Drive (VFD) traction control means more tonnes (tons) produced per shift due to improved sumping and relocation times and a faster tram speed of up to 26 m/min (85 ft/min) (governed).
BENEFITS AND FEATURES
Cutter Head The cutter head on a continuous miner uses up to dual 250 kW (335 hp) 2 × 209 kW (280 hp) motors to cut material. The head typically consists of three pieces: the right drum, left drum, and center drum. Drum diameter is optional (1066-1168 mm/42-46 in), as is drum speed (42-52 rpm).
Motor Protection The cutter motors are protected by torque-limiting clutches designed to respond within 1/10th of a second. Massive 152 mm (6 in) boom legs on the cutter support the frame and ensure minimal deflection and fatigue. The cutter drums are 50.8 mm (2 in) thick, allowing maximum bit-tip standoff.
Split Gear Case The cutter gear case is split. Each side is independent and only connected by the center cutting drum. This allows one gear case - with half the number of components - to be replaced.
BENEFITS AND FEATURES
Gathering Head The CM400 Series offers a variety of 3-finger centrifugal loading arms (CLAs) to meet customer requirements as well as a choice of three chain and CLA speeds. 6-finger CLAs - found to be 40% more effective in low seams - are also available. The gathering head assembly has a chromium-carbide overlay (CCO) wear protection package.
Conveyor The CM445 has 965 mm (38 in) or 762 mm (30 in) wide conveyor for fast loading. The high-strength 69.85 mm (2.75 in) Cincinnati conveyor chain is driven by an 8-tooth dual sprocket with universal joint for smooth, low-wear operation. An automatic hydraulic chain tensioning system reduces noise and further improves chain service life.
Wear Protection The top decking of the conveyor is CCO-plated (chromium-carbide overlay) and the return deck is plated with 450 BHN wear plate for greater wear protection. The conveyor has a 45-degree swing capability each way.
BENEFITS AND FEATURES
Ease of Operation The Cat Machine Control Unit (MCU) is designed to operate the entire Cat CM445. Based on a mine-duty PLC, this drive and control system combines maximized coal production and operator safety with minimum downtime. Traction motors are controlled by a microprocessor-based system, minimizing the connection points that are the major cause of downtime. The MCU provides data logging, fast diagnostics and enhanced troubleshooting capability.
Machine Management A comprehensive machine management and diagnostics system is used to manage the continuous miner’s health and aid in the quick diagnosis and repair of the problem.
Remote Control A Super Simpson radio remote with self-diagnostics is available. Features include:
- Graphic display shows the condition of all motors, VFD components, and the condition and position of all hydraulic control valves and solenoids.
- Tito remote control console or new compact remote control console
- Motor Mate AC current sensor
BENEFITS AND FEATURES
Enhanced Performance with VFD Variable Frequency Drive (VFD) traction control means greater tonnage produced per shift due to improved sumping and relocation times and a faster tram speed of up to 26 m/min (85 ft/min) (governed). VFD also means
- Greater system efficiency
- Reduced cost of motors
- Ease of troubleshooting
More Torque VFD provides more motor torque across the entire traction speed range.
Brushless Motor Design This translates into less maintenance and longer motor service life.
Pays for Itself VFD pays for itself through higher extraction and lower maintenance costs over its 1.79 million tonne (2 million ton) service life.
BENEFITS AND FEATURES
Safety Cat mining machines and systems are designed with safety as their first priority. The control system is proximity detection ready (details below). The intuitive human machine interface gives the operator and maintenance supervisor an unprecedented level of understanding of their machine. The dual-sprocket conveyor chain drive results in lower ambient noise, while the hydraulic temperature and spool position monitoring (via CAN bus) herald a new level of safety as the machine can identify points of failure and recognize valve malfunction.
Proximity Detection Caterpillar has developed a Personnel Proximity Detection System with the aim of clearly identifying the presence or absence of personnel reliably and with high repetition accuracy, and of transmitting this information in real time to the local control system to allow appropriate action to be taken to prevent injury. The machine controls can be configured to give different responses to encroachment into the various zones, such as warning, reduced speed and shutdown. A silent zone can overlay the red zone, allowing the operator to see the cutter while staying out of the turning radius of CM. The fields can be customized to provide different-shaped fields.
Other Safety Features These include a dust collector, scrubber, dust ignition protection, water solenoid valve to minimize water use and spillage, methane monitoring and noise reduction.
BENEFITS AND FEATURES
Service-Friendly In addition to long overhaul intervals and wear-resistance features, the CM445 has a number of features to simplify maintenance and repair:
Preventive Maintenance Caterpillar’s thorough preventive maintenance program ensures that the integrity of the machine is not compromised. When properly maintained, Cat continuous miners perform for years at lower maintenance costs, thus lowering the total cost of ownership.
Easy Access
- Centralized location of grease points and fill ports for ease of maintenance
- Ease of access to cutter head gear oil checks and replacement
- Cutter head motor mounting location allows easier access for replacement
Resistant to Wear
- Astralloy-V crawler frame wear liners
- Chromium-carbide overlay (CCO) wear protection package for cutting head gear case struts
- 3- or 6-finger centrifugal loading arms (CLA) with replaceable bolt-on wear tips
- Chromium-carbide overlay (CCO) wear protection package for gathering head assembly
- The top decking of the conveyor is CCO plated and the return deck is plated with 450 BHN wear plate
- Heat treated alloy steel crawler pads for wear resistance and 100% increase in pivot wear area material
Split Gear Case The cutter gear case is split. Each side is independent and only connected by the center cutting drum. This allows one gear case - with half the number of components - to be replaced, as opposed to standard designs that require replacement of the entire assembly. The gear case has three independent oil compartments, allowing convenient viewing of oil levels through site gauges.
Slide from the Side The traction units are complete assemblies that slide in from the side. VFD motors are brushless motor design, requiring less maintenance and ensuring longer motor life.